Returning home from travel in 2017, I had cracked my Zipp disc and needed to find a replacement. This lead me to doing some research on the different wheels available, and the tech which went into them. This ultimately led me to Caden wheels (lightweight, wide, high temp resins, good profile and also at half the price of similar equivalents).
Skeptical at first, given them being relatively new on the scene, and without seeing a bunch of marketing as per the big brands, I reached out to get some more information. Ben, the owner/creator of Caden was extremely knowledgable. The more information I got, the better they stacked up, and the more I learnt. Switching from my 808’s to Caden’s equivalent saved me over 400grams, and about $2000.
I have since been able to build a relationship with Caden and been a part of the development of wheels. This has really shown me how much goes into a carbon wheelset, and that they are all far from created equally. I am writing this piece more as some things to think about, and investigate, when buying carbon wheels, as opposed to a plug for Caden.
Moulds
Open moulds are owned by the factory and used to create a generic rim, which is available to everyone. Closed moulds are owned by the Wheel company and used for their rims only. This gives them control over the wheel profile and the condition of the mould. When moulds are used a lot of times they can develop wobbles and produce not entirely round rims. Closed moulds are a lot more expensive and have much bigger minimum orders, but ultimately allow a lot more quality control of the rims produced.
Caden have their own moulds (closed), as would be the case for most premium wheel lines.
Bladders are used to form the rim, removal of this bladder is done in different ways. Some manufactures join the rim in pieces, some cut a hole in the rim bed, and some have a system to remove the bladder with no holes (Caden).
Braking Surface
The characteristics of the resins used dictates their heat performance. Factory's with high temperature molding can produce rims with a much higher heat tolerance. This is especially important for long descents and extensive braking, which will cause the rim to heat significantly. This is is a major problem on many cheap rims, where the heat exceed the resin curing temperature. There have been many cases of exploding front wheels, due to excessive brake track heat!
Caden rims are made at a high temp factory, they heat test the brake tracks to 250 degrees Celsius. Ben personally tested the wheels on long descents in Thredbo with a 40kg back pack!
The type of carbon, and direction of carbon in the brake track makes a big difference to not only its durability but also its braking modulation. Caden uses toe preg carbon run in the direction of the braking, hence braking is with the grain of the fiber. Carbon is very strong in tension and thus orientating the fibres in direction of the braking with no kinks improves braking modulation significantly.
Interesting video here of Ben at the factory explaining: https://www.youtube.com/watch?v=VOX5NjomPUQ
Clincher Hook Formation
Creating carbon clinchers took some time initially, the force induced on the rim edge was hard to resist with carbon fibres. The formation of this hook is crucial to its strength. Caden form a full section across the top of the wheel in the molding process, before cutting out the channel creating undisturbed fibres on the hook.
Another good video from Ben showing the above from the rim factory: https://www.youtube.com/watch?v=yN0E_-p4JrA
Layup
Layups can have a big influence on the weight of the rim. Many manufacturers skip some additional steps they can take to optimise the layup. The areas of the nipple are high stress points, and hence require more carbon that those areas of the rim edge with no nipple. Removing excess material and just adding it at the nipples optimises the rim weight (Nipple patching). Caden wheels use nipple patching, which is an additional manufacturing cost, but one which allows their wheels to be extremely light, whilst remaining safe.
Profile
The last few years has seen a shift in profile shapes. Historically, narrow was deemed fastest. However with changes in tyre technology and the move to wider tyre preferences for rolling resistance, rim manufactures have been following suit. A fat tyre on a narrow rim in slow, but when the complete system forms a aerodynamic profile it is a lot better. Ideally the rim should be slightly wider than the tyre. If you plan on using wide tyres, ensure you get a wide profiled wheel to suit!
Caden latest iteration are using 27-28mm wide rims. They also have a very deep tyre bed, to create as smooth a profile as possible from rim to tyre.

Hubs/Spokes
My personal belief is that the most simplistic and balanced spoke/hub arrangement is the best. There has been many people trying to reinvent the wheel over the years, with the likes of paired spokes etc. But it keeps coming back to the radial formation on the front wheel and the 2:1 ratio on the rear wheel. Caden sticks to this tried and true method.
Kinks/bends in the spokes also creates weak points. Straight pull Sapim spokes are utilised on Caden. They have also stuck with external nipples. The purpose of this was to eliminate the bend you get when the spoke enters the rim to an internal nipple, plus also makes for easy serviceability. Although not as clean looking as an internal nipple.
Hub material quality is important. Caden hubs are made in the factory with one of the biggest wheel manufacturers (Sram/Zipp). They are one of the only places able to do 3D Forged T7075 aluminium. T7075 is a stronger grade of aluminium which is more capable of resisting the high stresses than the cheaper alloys.
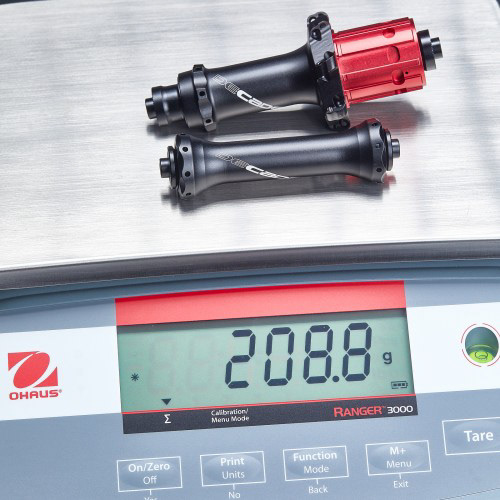
Weight
Wheel weights, claimed and actual can be very different things. Aero has become the new trump card and everyone has seemed to forget about weight as much. There are some major differences, well worth checking into! Especially for hilly races. Caden have achieved some super impressive weights eg ~940gram 25mm tubular wheelset.
Price
Premium carbon wheelsets are now costing a small fortune, with most in the $4-6k range. Most of the cheaper brands have taken some shortcuts in some parts of the manufacturing process above. Caden are still in the early days, they have been focusing on developing a top quality wheel, and now they need to shift wheels to cover that development. Hence they are selling direct to the consumer, and at an extremely competitive rate:
$1885 AUD inc Worldwide Delivery/Duties, Titanium Skewers, Decadence Upgrade, Brake pads, Rim tape glue (tubular).
See below for a quick comparison of some known brands weight & price:
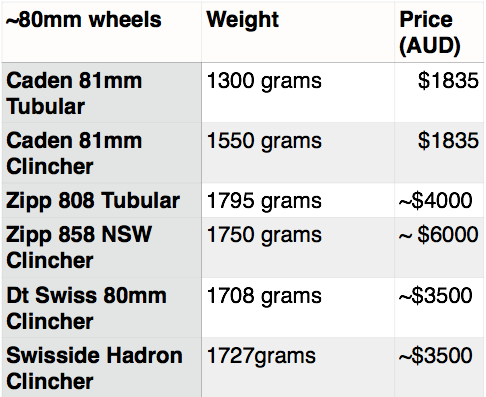
I hope this helps to give you some things to research before making your next wheel investment! If you want to know more about Caden, feel free to get in touch with myself or Ben.
Ben is a small fish competing against the big guys, if you want to support him or enquire about Caden wheels, feel free to check out: https://carbonbikewheels.com.au or email ride@carbonbikewheels.com.au.
Bonus.... There is also some new wheels on the way very shortly for the TT connoisseur. I have been on a prototype disc (~850 grams) and there is also a super slippery Tri Spoke on the way.